What is factory digitization?
5/5
The factory is the place where products are created, in other words this is the “heart” of the business. Only by producing goods will enterprises have a way to survive and develop. Therefore, investing in production and in factories is the most basic and sustainable investment. Businesses can spend a lot of money on marketing activities to promote product consumption, but always remember that the core factor for customers to return to your brand is always the quality and quantity of products. Every year, the number of businesses registering to enter the market is always in the tens of thousands. This means that the competition of the business is increasing day by day. The more new businesses are born, the more advantages they have in the application of information technology, technical transformation, digitization, etc.
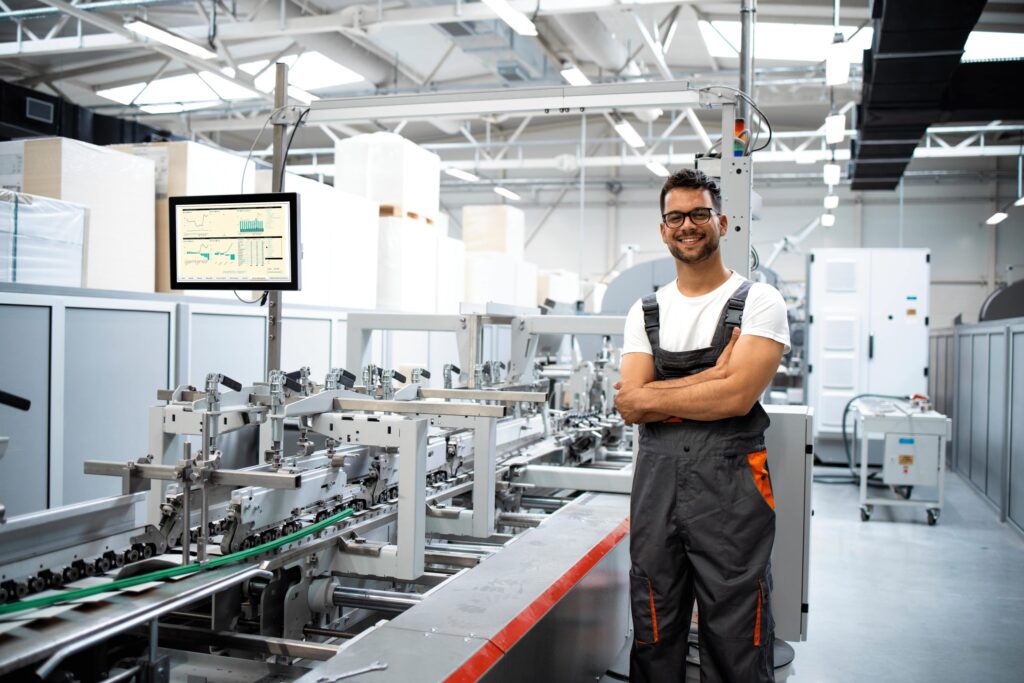
Before learning about the concept of digitization, you need to understand what conversion is? In the 4.0 technology revolution, transformation is considered one of the most important goals of the economy in particular and all other fields and industries in general. There are many concepts given when talking about digital transformation, but the concepts are all geared towards the application of modern information technology such as: Cloud computing platforms, Big Data, Internet of Things (IoT)… into the working environment of enterprises. In order to transform businesses from “traditional” to “modern” form, improve the quality and quantity of products.
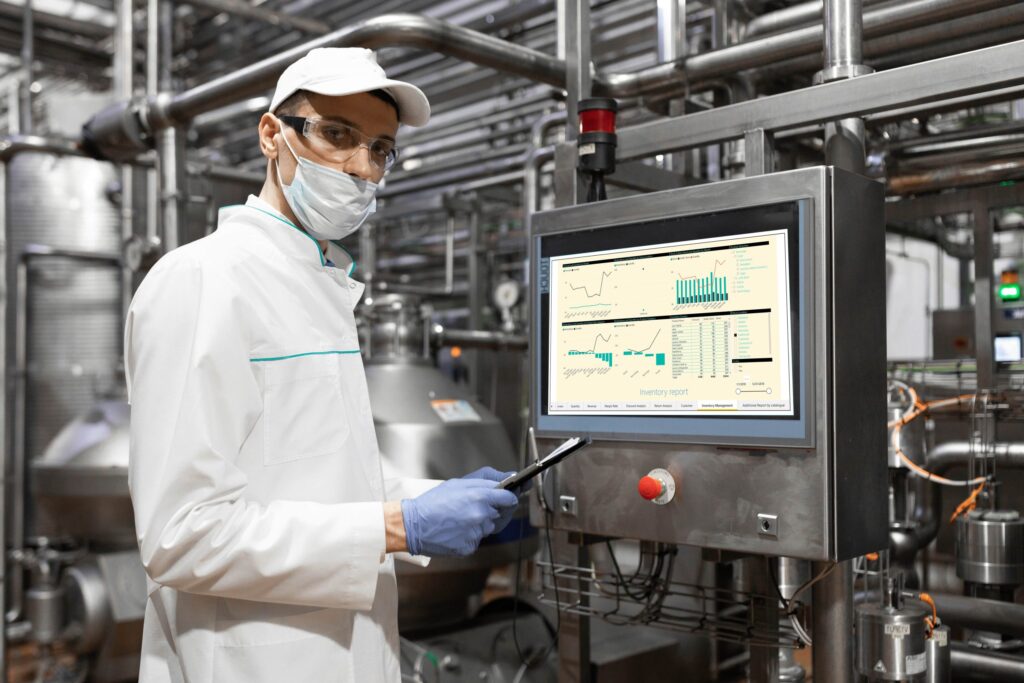
Digitization is seen as part of the transformation. The information and data will be stored in many different forms; According to the traditional way of working, it is mainly archived with papers, documents, forms… Digitization makes storage simpler, more accurate and more secure by converting information and data into formats. digital. Understood in a more general sense, digitization is the process of modernization aimed at transforming the working system from traditional, manual to modern, digital. Take a simple example: in the past, input material information of enterprises was usually stored on documents and papers and then uploaded to Excel files. With creative intelligence, all information will be formatted and stored on Factory Smart Forms & Checklists (technology solution of New Ocean Information System).
Factory digitizationis a category of digitization, in which the transformation towards modernity, digital is mainly applied to manufacturing factories.
Benefits of factory digitization
90%
From the content presented above, we can see that the number of new businesses born later is increasing. The 21st century is the era of information technology, artificial intelligence, Big Data… Not using these resources is a huge “waste” for your business. You may be apprehensive about the cost to invest in the conversion process. But if you consider the long-term strategy, this is definitely a “profitable” investment and a future trend. According to “Some solutions to improve production and business efficiency of processing industry enterprises in Ho Chi Minh City – Part II” copyright of the Institute of Research and Development of Ho Chi Minh City; Out of the 5 solutions offered, there are 2 mentioning the application of information technology.
So digitize the factory What are the benefits for businesses? The benefits outlined below will justify the question “Why is it necessary to digitize the factory as soon as possible?”
● Unify information and working data. Factory digitizationwill help to store relevant information and data such as input materials, output products, excess products, products in shortage, machine parameters… in a complete, logical and safe manner on technology background. For example, the Azure cloud platform of Factory Smart Forms & Checklists.
● Storing information in the technology space will minimize data entry errors caused by human factors during manual data entry. At the same time, the amount of data that can be stored is also very large. This is one of the most obvious benefits of doing so factory digitization.
● Factory digitization software, tools and solutionswill remind operators to maintain production machinery at the right time. Along with that, detecting and repairing machines when Downtime problems occur is also faster.
● Reduce unnecessary costs for businesses and factories. In the traditional working style, information, data, figures or even machine parameters are stored on papers and Excel files. This puts great pressure on businesses in terms of stationery costs, storage space as well as salaries for data entry staff.
● Shorten production time while improving product quality. The faster the paperwork, the faster the maintenance of the machines will facilitate the early start of the production process. This saves your business time and money.
● Increase your site’s edge over your competitors. The rapid absorption and application of technology shows that the ability of enterprises to explore and learn is great. The speed of technology is much faster than we can imagine if your factory and business apply it properly. Along with that, businesses will be able to show their progressive spirit to partners.
The above are the most basic benefits that your business will get when doing this factory digitization. This benefit will be even more if you find the right solution provider factory digitization.
New Ocean Information System (NOIS)
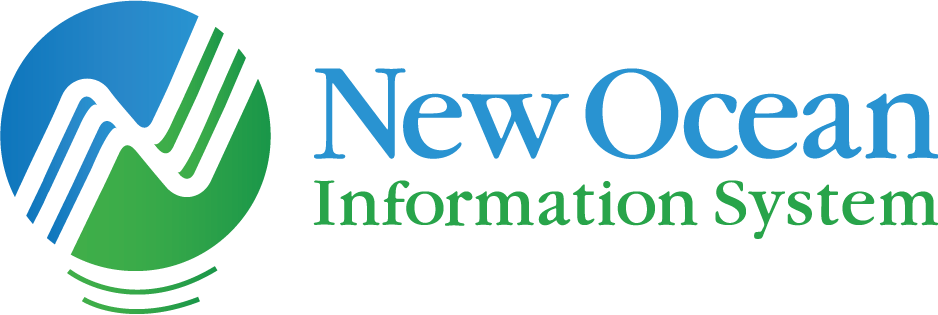
New Ocean Information System (NOIS) is proud to be a provider of technology solutions to support business digitization and digital transformation. During 12 years of operation with many successful projects such as Traceability, Supply Chain, Warehouse Management… New Ocean IS has cooperated with more than 70+ units large and small. Dedicated and professional in each project, NOIS brings satisfaction to customers with each product that helps businesses transform. After each project, the technology resources of New Ocean Information System continue to be expanded, creating a premise for the next development projects. The most recent hit project developed by NOIS is Factory Smart Forms & Checklists. Factory Smart Forms & Checklists is a comprehensive technology solution that doesn’t just stop at the goal factory digitization, properly exploiting FASF also helps your business convert digitally quickly and efficiently.
How does Factory Smart Form & Checklist (FASF) operate factory digitization?
● Unifying information and working data; Leaders, operators easily work with real-time information
● Data storage in the technology space
● Leaders, operators easily work with real time
● Check, remind machine maintenance time, Downtime problem and how to solve it
● Eliminate unnecessary paperwork, reduce unnecessary costs for businesses
● Shorten production time while improving product quality
● Increase your site’s edge over your competitors
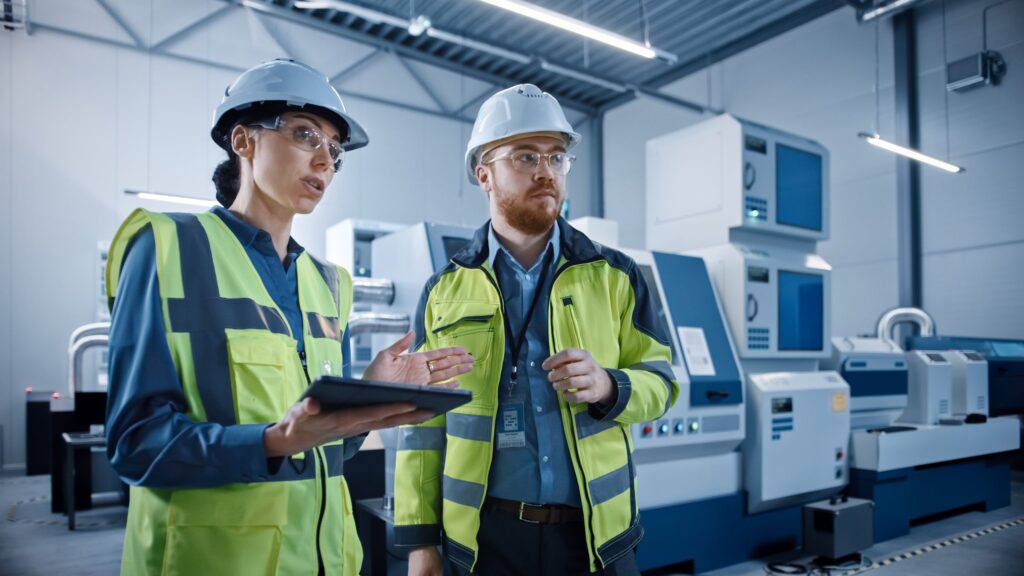
Surely when you follow the article here, you are wondering how Factory Smart Forms & Checklists (FASF) has implemented digital transformation in production, right? Let’s find out now.
Traditional | Digital conversion with FASF | |
Pre-production stage | Prepare warehouse: location, size, and storage capacity will be checked and recorded in documents, then input data into Excel file. Input of production materials: volume, weight, volume … input materials are stored in documents and then entered into Excel. Inspection of production machinery: comparing documents between the previous period and the next period, difficulties in grasping the technical parameters of the machines as well as the maintenance time. | Prepare warehouse: all information related to the warehouse has been stored in FASF software. You just need to open the software and compare the parameters. If anything changes, please proceed to update more. Input of production materials: with just one simple operation all necessary information is in FASF. Checking and controlling is easier than ever. Check production machines: You just need to use a smart electronic device to scan the QR code that has been integrated on the production machinery. The necessary information will appear immediately |
Stage in production | Downtime problem: Unexpected downtime, it takes a while for repair staff as well as management levels to grasp the information. Productivity of production machinery: if you want to know if a machine is producing according to its capacity, you need to find out the technical parameters of the machine as well as the production capacity in the previous runs. | Downtime problem: when downtime occurs, repairmen and operators immediately receive information through the Factory Smart Forms & Checklists system (specifically here is email). In the meantime, technicians and operators can rely on the error library built into FAS. Productivity of production machines: just like the process of checking production machines, you just need to scan the QR code and all the necessary information will appear. |
Post-production stage | Goods out of stock: quantity, information is recorded on forms, paper forms then pushed up and stored on Excel file. Goods left over, lost: the process of checking and counting takes place manually. Sometimes this is not effective, the amount of residual goods is unknown and the amount of lost products is not captured. | Goods out of stock: right from the production stage, the results of the production process are stored on the FASF. After the goods are released from the warehouse, the latest parameters will also be quickly updated to the system. Goods left over, lost: as mentioned above, the goods parameters are stored in parallel with each stage. You just need to check to know how much goods are in stock and whether there is a loss or not. |
You can imagine the process of FASF operating the factory digitization as follows
- The first customer to use the Factory Smart Forms & Checklists solution of NOIS is Vinamilk (a brand of Vietnam Dairy Products Joint Stock Company). Later realized the great potential of FASF in factory digitization, digital transformation in many different fields, NOIS has researched and developed FASF based on the unique characteristics of each industry.
- Factory digitizationIn pre-production preparation
– Data entry: Quantity, volume, volume… of materials used in production will be entered and stored securely into the FASF system. At the same time, the warehouse information containing raw materials and finished products is also stored with full information from address to capacity.
– Inspection and maintenance of production machinery: On each production machine, there will be a QR Code. Maintenance staff only need to use an iPad
with built-in Factory Smart Forms & Checklists software to scan the code. At this time, the information of the machine will appear from parameters, machine data, operating time …
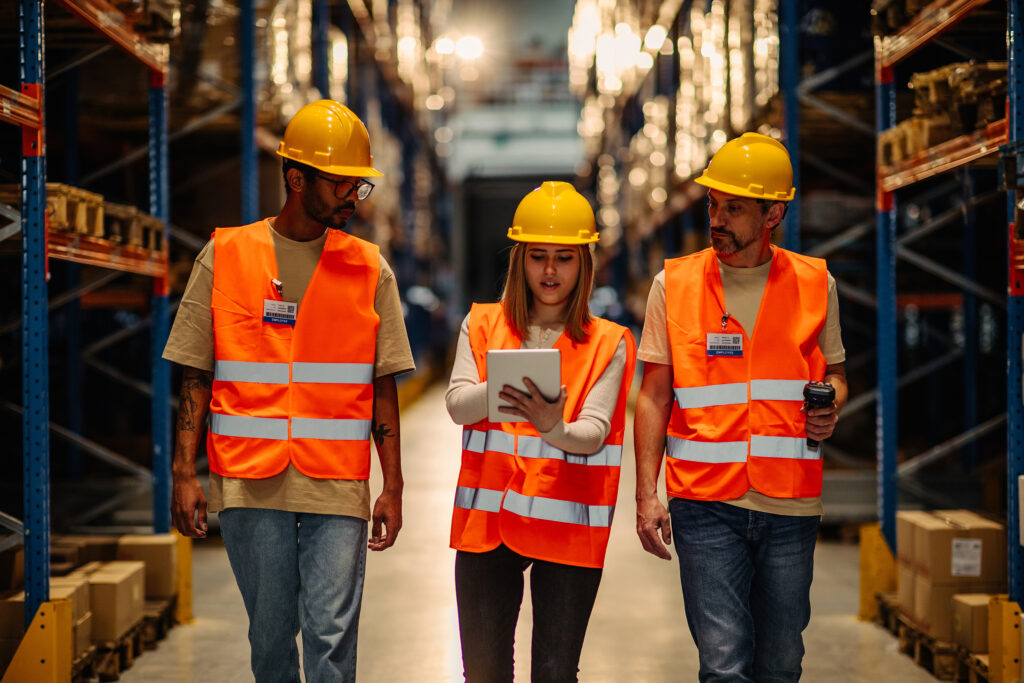
● Factory digitization in production: During production, sometimes there will be Downtime problem. At this time, FASF will use the Email system to inform necessary objects such as field operators, maintenance staff, and managers at all levels. While waiting for technical staff to come to repair, you can also use the previously updated error library system on FASF based on the Downtime errors that have occurred.
● Post-production factory digitization: It is very easy to lose product or not accurately control excess product. Using Factory Smart Forms & Checklists your business will not encounter such situations anymore. Besides, checking how many orders have been shipped or how many products have left the warehouse will take place quickly and accurately.
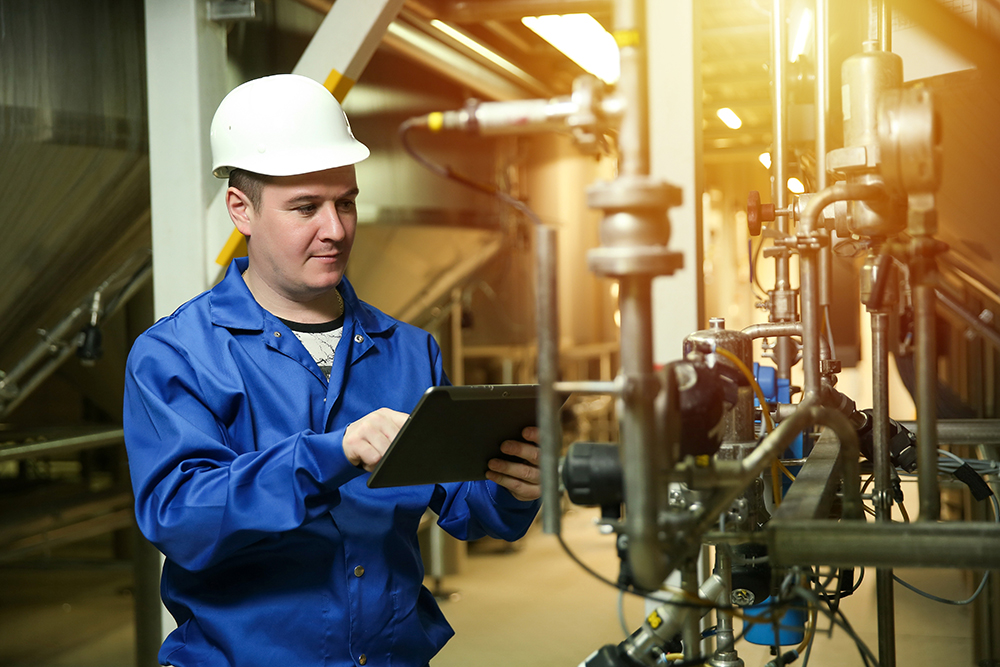
New Ocean IS & factory digitization understanding
In the industrial revolution 4.0, factory digitizationis the inevitable production trend. Modern innovation must go up from the most core production stage to create sustainable quality, quantity and productivity for factories and businesses. If your business stands outside this race, then you are missing out on your own growth opportunities. Let New Ocean Information System and Factory Smart Forms & Checklists accompany your business on the way factory digitization
✅ Số hóa được xem là một phần của chuyển đổi hóa. Các thông tin, dữ liệu sẽ được lưu trữ dưới nhiều hình thức khác nhau; theo cách làm việc truyền thống chủ yếu là lưu trữ bằng giấy tờ, văn bản, form mẫu… Số hóa giúp việc lưu trữ trở nên đơn giản, chính xác và bảo mật hơn bằng cách chuyển đổi thông tin, dữ liệu sang định dạng kỹ thuật số. Hiểu theo nghĩa khái quát hơn, số hóa là quá trình hiện đại hóa nhằm chuyển đổi hệ thống làm việc từ truyền thống, thủ công sang hiện đại, kỹ thuật số.
Thống nhất thông tin, dữ liệu làm việc. Số hóa nhà máy sẽ giúp việc lưu trữ các thông tin, dữ liệu liên quan như nguyên liệu đầu vào, sản phẩm đầu ra, sản phẩm dư thừa, sản phẩm thiếu hụt, thông số máy móc… một cách đầy đủ, logic và an toàn trên các nền tảng công nghệ. Ví dụ như nền tảng đám mây Azure của Factory Smart Forms & Checklists.
➡ Việc lưu trữ thông tin trong không gian công nghệ sẽ hạn chế đến mức tối đa các sai sót nhập liệu do yếu tố con người trong quá trình nhập liệu bằng tay. Đồng thời khối lượng dữ liệu có thể lưu trữ được cũng rất lớn. Đây chính là một trong những lợi ích dễ dàng nhận thấy nhất khi thực hiện số hóa nhà máy .
➡ Việc lưu trữ thông tin trong không gian công nghệ sẽ hạn chế đến mức tối đa các sai sót nhập liệu do yếu tố con người trong quá trình nhập liệu bằng tay. Đồng thời khối lượng dữ liệu có thể lưu trữ được cũng rất lớn. Đây chính là một trong những lợi ích dễ dàng nhận thấy nhất khi thực hiện số hóa nhà máy .
➡ Các phần mềm, công cụ, giải pháp số hóa nhà máy sẽ nhắc nhở nhân viên vận hành bảo dưỡng máy móc sản xuất đúng thời điểm. Cùng với đó, việc phát hiện và sửa chữa máy móc khi xảy ra vấn đề Downtime cũng nhanh chóng hơn.
✅ Trong cuộc cách mạng công nghiệp 4.0 số hóa nhà máy là xu hướng sản xuất tất yếu. Sự cải tiến hiện đại phải đi lên từ khâu sản xuất cốt lõi nhất mới tạo ra được chất lượng, số lượng và năng suất bền vững cho nhà máy cũng như doanh nghiệp. Nếu doanh nghiệp của bạn đứng bên ngoài cuộc đua này, thì chính các bạn đang tự đánh mất đi cơ hội phát triển của mình. Hãy để New Ocean Information System và Factory Smart Forms & Checklists đồng hành cùng doanh nghiệp của bạn trên chặng đường số hóa nhà máy nhé!