Optimizing Production with Optix (Rockwell Automation) for Comprehensive Data Collection
As the manufacturing industry undergoes a strong digital transformation, data collection and analysis are crucial for enhancing efficiency, optimizing processes, and making data-driven decisions. Optix Rockwell, with its flexible and robust connectivity, combined with NOIS’s comprehensive data collection solutions, provides an optimal solution for manufacturing plants.
Integration and Data Collection Process
- Diverse Connectivity: Optix, with its superior connectivity, easily accesses and collects data from a variety of devices and environments within the factory, including PLCs, controllers, OPC Servers, and more.
- Centralized Data Storage: Collected data is stored centrally and securely in the system’s database.
- Intuitive Dashboard: A custom website developed by NOIS utilizes data from the database to create an intuitive OEE (Overall Equipment Effectiveness) dashboard, enabling managers to easily monitor and evaluate factory performance.
- Automated Data Entry: Operational data is automatically populated into electronic forms, minimizing manual data entry and increasing data accuracy.
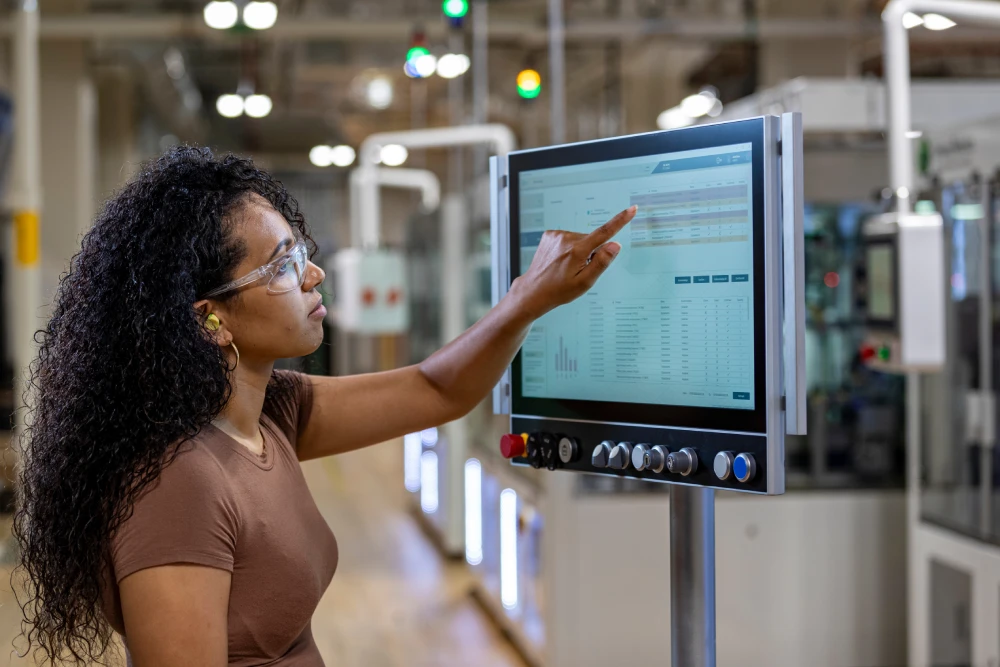
Real-World Example
To illustrate this process, let’s consider a practical example with Vali PLC, a system of 4 PLCs used to simulate data from production machines in a factory.
- Raw Data Collection: Operational data from sensors on production machines is collected.
- Data Processing and Separation: Raw data is processed, separated, and supplemented with machine IDs and data transmission timestamps to Optix.
- PLC Connection and Data Collection: Optix Runtime, running on a PC, connects and collects data from various PLCs.
- Database Data Storage: Collected data is entered into the Optix database, ensuring integrity and readiness for subsequent steps.
- Data Retrieval and Utilization
- Independent Storage: Optix data is stored independently, providing flexibility in access and usage.
- Raw Data Creation: The DxFAC Database proactively retrieves data from the Optix Database to create raw data.
- Data Synchronization: Raw data is synchronized into data forms, reducing VHM (possibly an operational management system or process) data entry.
- Data Aggregation: The DxFAC Database aggregates data from VHM input to create complete data.
- Analysis and Statistics: Depending on user preferences, the system can use raw data, data forms, or a combination of both to generate OEE statistics, machine downtime statistics with causes, or defective product statistics.
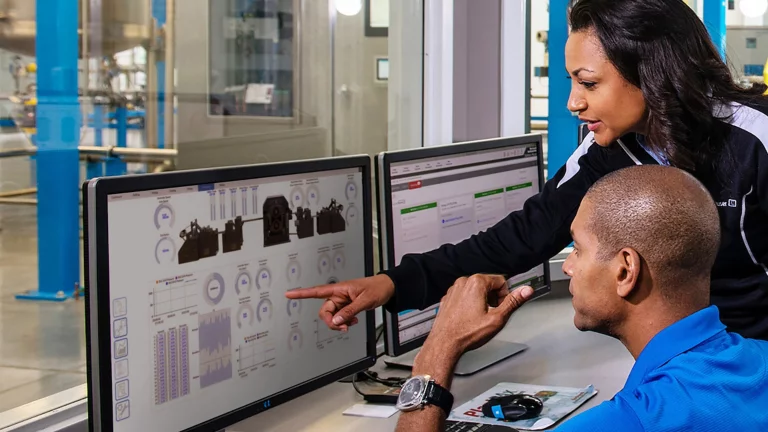
Solution Benefits
- Performance Optimization: Helps factories gain detailed insights into production operations, enabling improvement and performance optimization measures.
- Cost Reduction: Minimizes manual data entry, saving time and costs.
- Enhanced Accuracy: Data is collected and processed automatically, reducing human error.
- Data-Driven Decision Making: Provides accurate and timely information for managers to make data-driven decisions.
Conclusion
With the combination of Optix Rockwell and NOIS’s data collection solutions, manufacturing plants can leverage the full power of data to enhance operational efficiency, optimize processes, and gain a competitive edge in the market.
This article provides an overview of the Optix Rockwell integration process for connecting controllers to retrieve data. If you have any questions, please don’t hesitate to contact us for consultation and support.
For more information, please contact us:
New Ocean IS:
- Website: https://nois.vn/
- Digital transformation solution package: https://dxfac.com/